The disrupted global supply chain has been making headlines for over two years, heightened by continued economic uncertainty, enduring effects of the COVID-19 pandemic and geopolitical conflicts like the Ukraine-Russia war.
Hardest hit industries include healthcare, retail and manufacturing. In fact, 80% of manufacturers have experienced a significant supply chain disruption in the past 12-18 months. The majority of those companies also reported profit decreases of up to 13%, stemming from issues such as shipping delays, raw material shortages and transportation shocks.
When coupled with other supply-related risks, such as extreme weather and the recent spike in cyber attacks, it’s clear that businesses should expect to face another major supply chain disruption like that of the global pandemic.
While it’s difficult to predict what the next big disruption will be, it’s important for business leaders to understand what the future supply chain will look like and how they can strengthen their organizations’ supply chain resilience.
Current state of supply chain disruption
Although the global pandemic was the impetus for a renewed focus on supply chain resilience, a range of small and large scale supply chain shocks are reverberating across the globe and continuing to test companies and their security and risk management capabilities—from cargo damage and port congestion to labor shortages and cyber attacks. Organizations must also contend with rising costs and inflation that not only undercut revenue, but also threaten to put their key suppliers out of business.
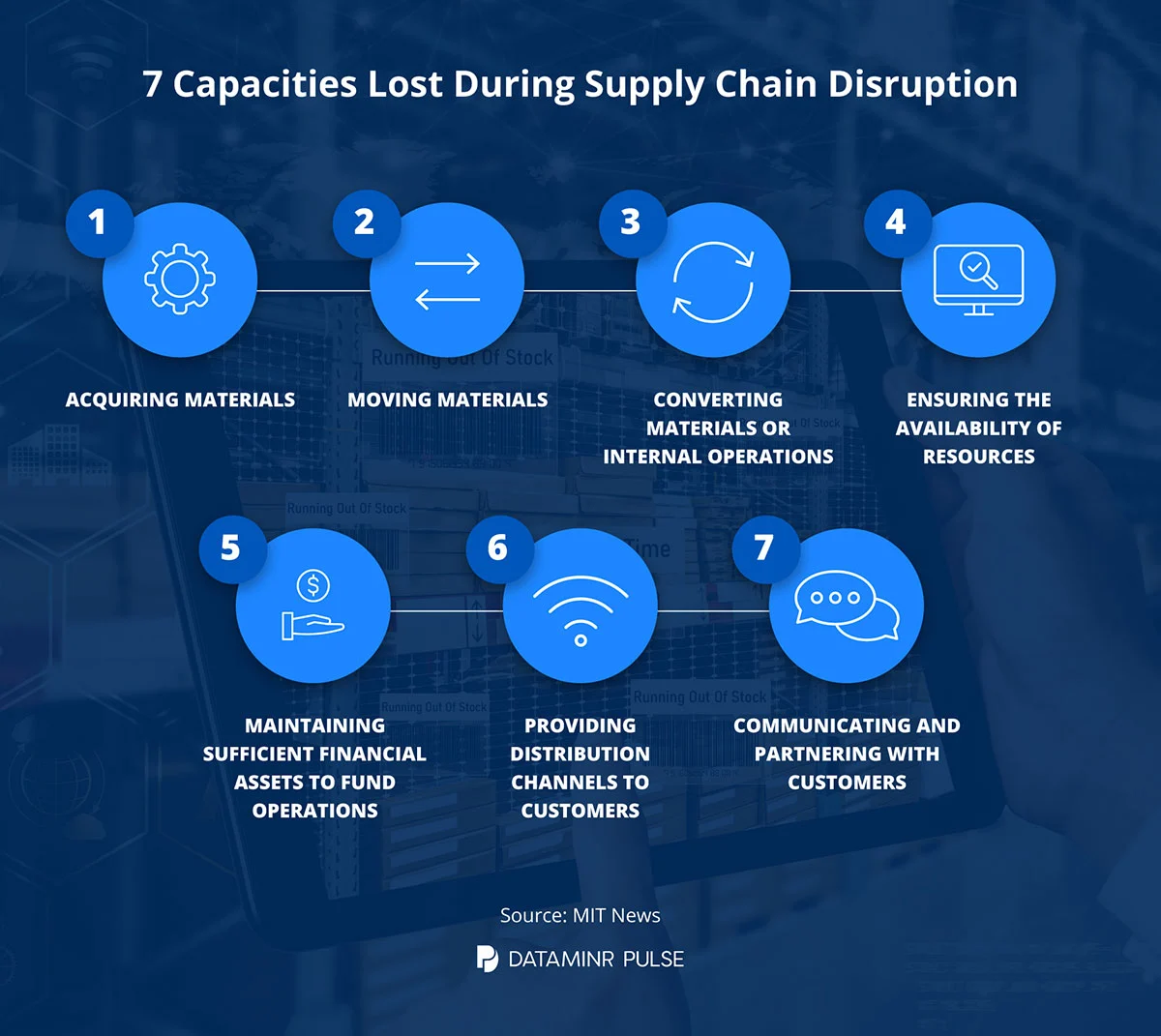
To help minimize the impact of supply chain disruptions, it’s important for all business leaders—but particularly supply chain, security and risk leaders—to understand these five key areas of supply chain disruptions.
Geopolitical uncertainty
Geopolitics have always been a source of potential disruption, but conflicts like the Russia-Ukraine war have become a major risk to global supply chains. According to Dun & Bradstreet, at least 374,000 businesses worldwide rely on Russian suppliers; more than 93% are based in the U.S. and at least 390 businesses globally have critical suppliers in Russia. The majority are based in one of five countries: China, India, Japan, the United Arab Emirates and the United States.
Given how interconnected our world is, a geopolitical issue in one country can have cascading effects on supply chains around the world, across various industries.
For example, rising tensions between China and Taiwan are pressuring western manufacturers to find alternative supply sources. After former U.S. House Speaker Nancy Pelosi visited Taiwan in April 2022, Chinese military exercises in the region disrupted one the world’s busiest global trade routes. The maneuvers temporarily shut down shipping routes and canceled more than 400 flights at major airports, interrupting 18 international air routes.
Resource shortages
With a scarcity of workers to fill open positions, supply chain leaders are struggling to maintain productivity amid rising consumer demand. An ongoing labor shortage in Europe’s trucking industry, for instance, is expected to worsen in the coming years. According to an IRU report, the region could be without over two million truck drivers by 2026, which is triple the current rate of unfilled positions.
Meanwhile, supply shortages have generated significant bottlenecks for companies in the technology and auto industries. A global microchip shortage upended production in these industries over the past few years, greatly curtailing supply chains and delaying the delivery cycle.
Extreme weather events
The effects of climate change manifest themselves in countless ways, from record-high temperatures to unprecedented weather events. Many of these manifestations also present supply chain challenges the likes of which businesses have never seen before.
Take the Rhine River, for example. Heavy rainfall and snowmelt in 2021 caused extreme water fluctuations in the river, which is one of Europe’s most important commercial waterways. When river banks began to burst, shipping halted for several days. Later that year, a drought greatly reduced shipping capacity and disrupted both inbound raw material and outbound product deliveries.
Port closures
When global trade routes are congested, it comes at a serious cost to organizations and their supply chain partners. Surges in demand for supplies may lead to clogged ports, disrupted trade flows and ships forced to navigate tight waters.
This is exactly what happened when the Ever Given container ship blocked the Suez Canal in March 2021. The blockage temporarily prevented 369 ships from passing through the canal, causing oil prices to rise by 5.77% and costing approximately $9.6 billion in trade each day.
Preparing for these five key areas of supply chain disruption calls for early risk detection. That’s when real-time alerting solutions like Dataminr Pulse play a critical role. They ensure organizations are made aware of potential risks and disruptions that could impact not just their supply chain, but that of their suppliers. The sooner they know about such risks, the sooner they can mitigate them and take action to maintain business continuity.
For example, when a fire at a plastic factory in Dubai, UAE, occurred in June 2021, Dataminr Pulse provided early warnings with clear images, giving customers more than one hour of lead-time to contact suppliers, reroute stock from distribution centers and assess supply chain viability.
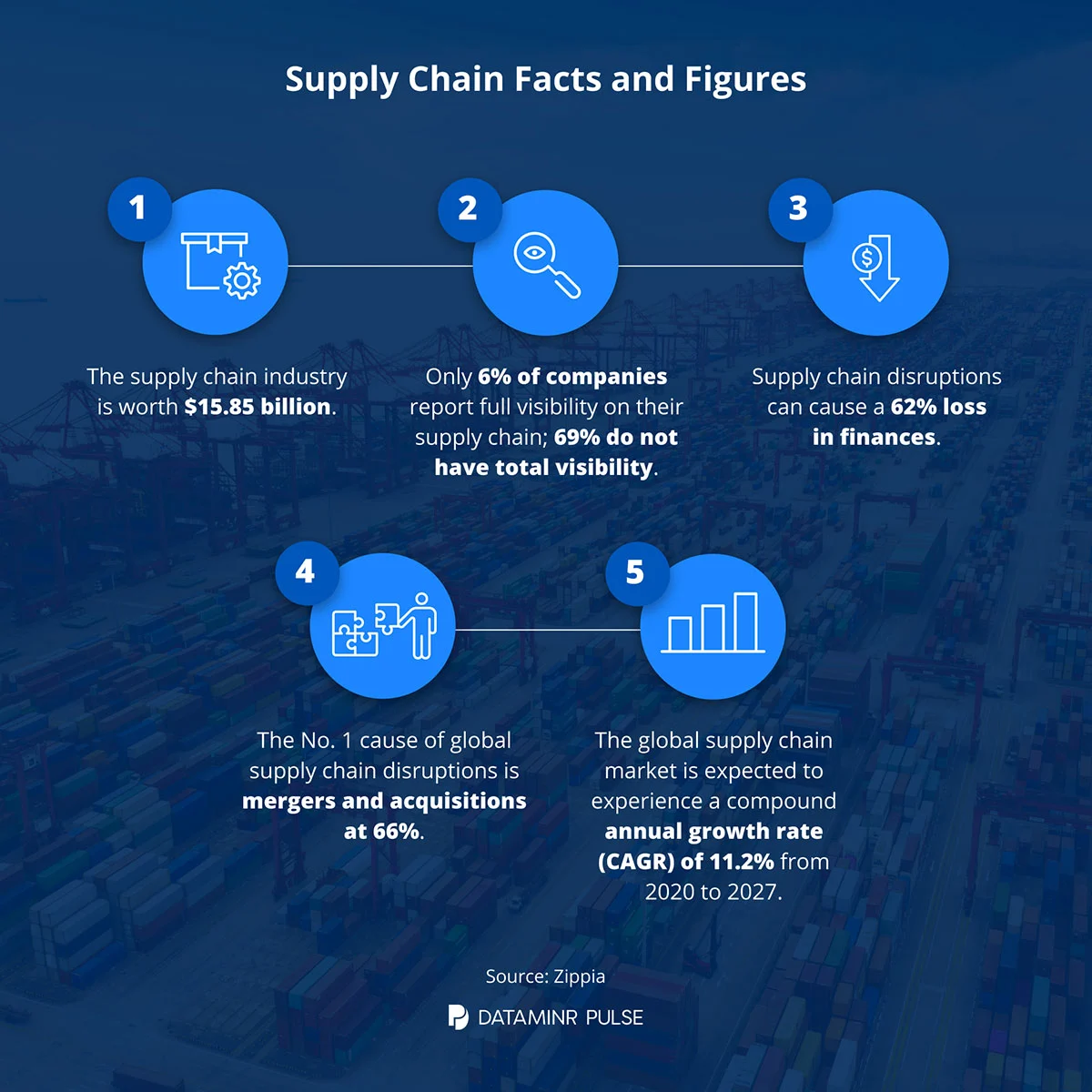
Supply chain outlook
In 2023, organizations will continue to face a host of supply chain challenges. These challenges will include disruptions that are a combination of lingering pandemic-related issues and compounding events, according to J.P. Morgan.
- COVID lockdowns in China: As the country doubles down on its strict lockdown restrictions, China’s policies are expected to further disrupt its manufacturing and shipping output. Guangzhou, China’s manufacturing hub, became the epicenter of its latest outbreak in November, which prompted stay-at-home orders and interrupted global supply chains. With no signs of China abandoning its zero-COVID approach, similar supply chain issues may persist in 2023.
- Port congestion: When Chinese output resumes, major international ports in the United States, United Kingdom and other countries may face congested shipping lanes. With more ships waiting for trucks to move containers, overcrowded routes may delay delivery times, increase overhead costs and raise the risk of cargo theft and/or damage.
- Spillover effects of the Russia-Ukraine conflict: As is the case with any geopolitical conflict, events may impact supply chain operations, particularly those related to European ports and global trade routes. Accenture reports that supply chain disruptions arising from the Russia-Ukraine conflict could result in a €920 billion loss to gross domestic product across the Eurozone in 2023.
- Cyber crime focused on business disruption and reputational damage: According to the World Economic Forum, 91% of business leaders believe global geopolitical instability is moderately or very likely to lead to a catastrophic cyber event in the next two years. Forty-three percent think it is likely that in the next two years, a cyber attack will materially affect their organization.
5 strategies for supply chain resilience
McKinsey’s third annual survey of supply chain leaders around the world indicates that organizations are making moves to overcome disruptions, mitigate risks and build more resilient supply chains. In fact, 90% of organizations want to increase their supply chain resilience. Thus, many companies are planning significant changes to their risk management and supply chain strategies.
Here are five tactics business leaders can use to better absorb and response to global supply chain disruptions:
- Dual sourcing. Refers to the use of multiple suppliers for a given raw material instead of depending on an individual supplier. Adding redundancy reduces the likelihood that a supply disruption will significantly interrupt the flow of goods across the supply chain.
- Regionalization. Regionalized supply networks leverage near-shore supply chain partners, which can accelerate movement in regions close to organizations’ distribution streams—reducing delivery times. Regionalization also frees up cash that otherwise would be tied up in inventory.
- Increased inventory. Stocking up on raw materials can put organizations in a better position to mitigate a shortage. For example, after an earthquake struck Japan in 2011, Toyota began stockpiling semiconductors; its efforts paid off in 2020 when a microchip shortage derailed auto manufacturing globally.
- Event detection. Organizations need to be able to identify risks and critical events as soon as they occur. They can then mitigate and respond in real time, allowing them to maintain business continuity and minimize disruptions.
- Resiliency planning. Once organizations understand which threat vectors might disrupt their supply chains, they can prepare for likely scenarios. Planning includes effective crisis management, including documenting and coordinating response workflows for any given event and testing the effectiveness of response plans; this helps to uncover potential flaws and gaps.
Of the supply chain leaders surveyed by McKinsey, 97% said they’ve applied a combination of the first three strategies. And, 83% said that the measures they’ve taken helped minimize the impact of supply chain disruptions in 2022.
This progress is good news as the frequency and impact of supply chain disruptions is likely to continue into the foreseeable future. It is therefore incumbent upon organizations to be prepared for, not just the next big disruption, but any and all supply disruptions. Doing so has become more critical given how reliant organizations, countries and citizens are on one another.
Learn more about Dataminr Pulse and how its real-time information can be used to help organizations strengthen their supply chain resilience.
Risk in Real Time newsletter
Sign up for our monthly newsletter for the latest on security and business trends, news and insights.
SUBSCRIBE